Within the dynamic landscape of manufacturing machinery, the rapid evolution and strategic deployment of equipment stand as pivotal elements. These tools not only define the efficiency and quality of output but also embody technological progress shaping the industry.
This comprehensive guide delves into the multifaceted world of manufacturing equipment, shedding light on how these technological marvels are shaping the future of production.
What is a manufacturing machine?
Manufacturing equipment constitutes the bedrock of production processes, transforming raw materials into finished goods.
From rudimentary hand tools to intricate, high-cost industrial systems tailored for specific production line tasks, these machines are indispensable.
Their role in maintaining production rhythm and quality is paramount, ensuring manufacturers can adapt to evolving market demands.
The types of manufacturing device
Manufacturing processes rely on a vast assortment of machines, each with a specialized role. To comprehend the intricacies of contemporary manufacturing, understanding these tools is crucial.
This section offers a comprehensive catalog of manufacturing equipment employed in global product production.
Industrial storage tanks
Industrial storage tanks, meticulously engineered, play a pivotal role in the manufacturing sector. These sturdy containers are specifically crafted to house liquids and gases, serving as indispensable components in diverse industrial processes. Available in vertical and horizontal configurations, each tailored to accommodate various materials and spatial requirements.
Within manufacturing facilities, these tanks are extensively utilized to store raw materials or finished products, ensuring a continuous supply chain for seamless production operations. Their design often incorporates advanced features such as temperature regulation and pressure control, rendering them particularly suitable for handling sensitive substances.
Applications
- Chemical industry: Used for storing chemicals crucial to industrial processes.
- Automotive and energy sectors: Employed in holding water and oils vital for operational needs.
- Food and beverage industry: Provide temporary storage solutions for perishable goods.
- Pharmaceutical sector: Safeguard raw materials integral to pharmaceutical production.
Centrifuges
Centrifuges stand as indispensable tools within the arsenal of manufacturing equipment, leveraging their prowess in segregating components based on density. Operating on the principle of centrifugal force, these machines swiftly rotate materials to extract elements of varying densities.
They serve diverse roles across manufacturing, from disc nozzle centrifuges for precise separations to double cone configurations for more robust demands.
Within manufacturing contexts, centrifuges play a pivotal role in upholding product purity and quality. Their applications span critical functions such as separating solids from liquids in wastewater treatment and refining raw materials in the oil and gas sectors.
Applications
- Pharmaceutical industry: Essential for purification processes.
- Food and beverage production: Crucial for quality control measures.
- Chemical processing: Facilitates material separation tasks.
- Environmental management: Integral to wastewater treatment operations.
Industrial mixers
Industrial mixers are pivotal in diverse sectors, from food production to pharmaceuticals and beyond. These machines are essential for achieving uniformity and consistency in manufacturing processes by blending various components into a cohesive mixture.
These mixers encompass a wide array of types, ranging from double-arm mixers to drum tumblers, each designed to meet specific industry needs. They employ advanced technologies, from basic stirring mechanisms to sophisticated systems capable of handling a range of materials, including solids and liquids.
In manufacturing, industrial mixers are indispensable for creating homogeneous products, ensuring precision that directly influences the quality of the final output. They are crucial in industries where material consistency is paramount, guaranteeing optimal performance and product integrity.
Applications
- Food Industry: Blending ingredients to ensure uniform taste and texture.
- Pharmaceuticals: Mixing chemicals to achieve precise formulations.
- Automotive Sector: Blending paints for consistent color and finish.
- Plastics Manufacturing: Creating compounds with exact specifications for durability and performance.
Electric generators
Electric generators form an integral part of the manufacturing equipment ecosystem, providing essential power to sustain production processes. They are indispensable during power outages or in regions lacking reliable electricity supply. Generators come in various sizes and capacities, tailored for diverse industrial and commercial applications.
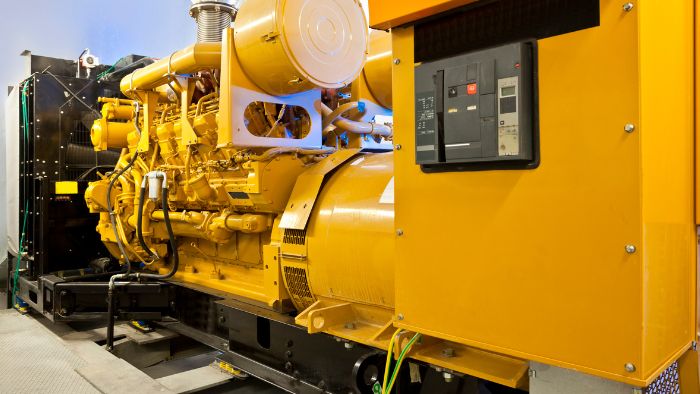
In manufacturing facilities, generators ensure the uninterrupted operation of machinery and equipment, safeguarding productivity and operational continuity. They are vital in critical areas such as assembly lines and machining centers, where consistent power supply is paramount for seamless operations.
Applications
Backup power in manufacturing plants: Ensuring continuous production during grid failures.
Remote construction sites: Power tools and equipment in off-grid locations.
Mining and drilling industries: Supporting operations in remote and rugged environments.
Data centers: Providing reliable backup power to safeguard against disruptions in digital operations.
Emergency services: Ensuring uninterrupted electricity supply for hospitals and emergency response centers.
Event management: Powering temporary setups and events with reliable electricity.
Compressors
Compressors are indispensable in the arsenal of manufacturing equipment, playing a critical role across diverse industrial applications.
They function by compressing air or gas to elevate its pressure, a principle pivotal in numerous manufacturing processes. The versatility of compressors is evident in their various types, such as rotary screw compressors for continuous operation in manufacturing plants and piston compressors ideal for intermittent use.
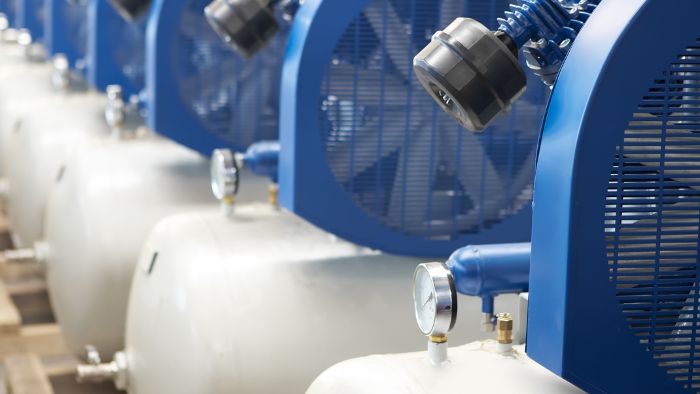
In manufacturing, compressors are essential for tasks requiring high-pressure air or gas, powering pneumatic tools, and supporting machinery operations. They are integral in precision processes like plastic molding, where maintaining exact air pressure is crucial for quality outputs.
Applications
- Automotive manufacturing: Operating pneumatic machinery for assembly and production lines.
- Construction industry: Powering handheld tools for construction and renovation projects.
- Plastic and rubber manufacturing: Essential for molding processes requiring precise air pressure control.
- Food and beverage industry: Used in packaging lines for sealing and processing operations.
- Oil and gas sector: Providing compressed air for drilling and extraction equipment.
- Medical equipment: Supporting air compression for medical devices and instruments.
Packaging equipment and machinery
Packaging equipment and machinery are essential components of the manufacturing sector, addressing the need for efficient and secure packaging of products. These systems range from manual tools to sophisticated automated solutions, including robotic packaging lines capable of handling diverse materials and packaging formats with precision.
These machines play a crucial role in ensuring products are packaged safely and attractively, significantly influencing their market appeal and consumer perception. In manufacturing facilities, they are indispensable for maintaining consistent and efficient packaging processes and meeting high market demands for both quality and quantity.
Applications
- Automated bottling lines: Used extensively in the beverage industry for precise filling and capping of bottles.
- Wrapping and sealing processes: Integral to the food sector for sealing freshness and ensuring product integrity.
- Box packaging: Essential in the consumer electronics industry for secure shipment and presentation.
- Pharmaceutical packaging: Critical for medication safety, compliance with regulatory standards, and ensuring product sterility.
- Labeling equipment: Incorporating labeling machines for accurate application of product information and branding.
- Cosmetics industry: Packaging delicate beauty products with precision and aesthetic appeal.
Shredders
Shredders in manufacturing are robust machines designed to shred materials into smaller, manageable pieces. They encompass a range of types, from industrial shredders capable of handling large volumes to specialized models tailored for specific materials such as metals or plastics.
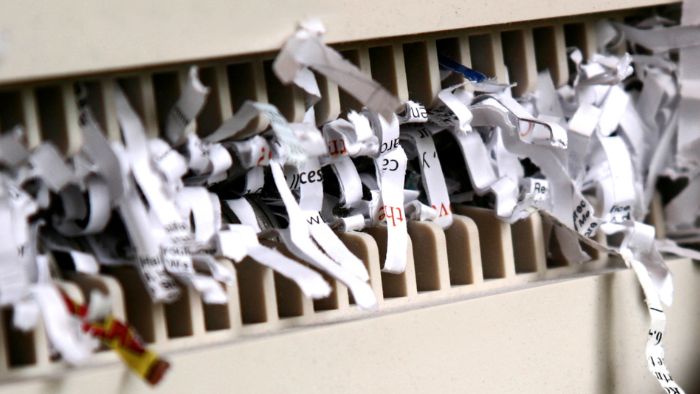
In manufacturing facilities, shredders play a pivotal role in waste management, recycling processes, and preparing raw materials for further use. Their efficient size reduction capabilities optimize manufacturing operations and ensure compliance with environmental standards.
Applications
- Recycling operations: Used across industries to process recyclable materials like paper, cardboard, and plastics.
- Waste management: Essential in manufacturing plants for shredding and compacting waste materials.
- Metal industry: Utilized to reduce the size of metal scrap for melting and recycling purposes.
- Automotive manufacturing: Processing scrap materials such as plastic components and metal parts.
- Textile recycling: Shredding fabric and textile materials for recycling into new products.
- Electronic waste (E-Waste) recycling: Breaking down electronic components for recovery of valuable materials.
Material handling equipment
Material handling equipment plays a pivotal role in the manufacturing sector, offering efficient solutions for transporting and managing materials within industrial facilities. This category encompasses a diverse array of tools and machinery, including forklifts designed for heavy lifting and conveyor systems for seamless product movement along assembly lines.
These machines are essential for maintaining a streamlined workflow and enhancing operational efficiency in manufacturing plants. By reducing manual handling, they significantly contribute to improved safety standards and heightened productivity.
Applications
- Transporting raw materials efficiently within warehouses, optimizing storage space and inventory management.
- Facilitating the smooth movement of finished goods to storage facilities or shipping areas, ensuring timely delivery and logistics.
- Integrating seamlessly into production lines to assemble and package products swiftly and accurately.
- Handling large and heavy components in demanding industries such as automotive manufacturing and aerospace, ensuring precise and safe material management throughout production processes.
Conveyor belts
Conveyor belts are indispensable in the manufacturing industry, serving a crucial role in transporting materials through various stages of production. Operating on a straightforward principle, these belts consist of continuous surfaces, typically made from materials like rubber or metal, which move over rollers to facilitate the seamless transportation of goods from one point to another.
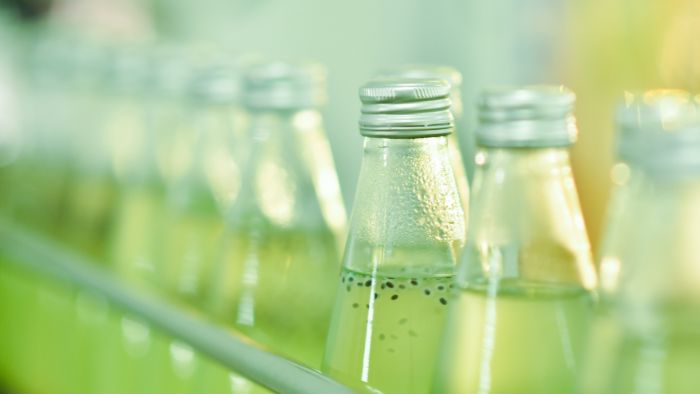
These belts are available in different types, such as flat belts for general transport and inclined belts for vertical or angled material movement.
In manufacturing facilities, conveyor belts are extensively utilized for their efficiency in consistently handling large volumes of goods. They are integral to assembly lines, packaging processes, and warehouse operations, ensuring uninterrupted flow throughout production.
Applications
- Facilitating the movement of products along assembly lines in automotive factories, optimizing production efficiency and workflow.
- Transporting raw materials within food processing plants, maintaining hygiene standards, and facilitating efficient manufacturing processes.
- Handling baggage efficiently and securely in airports, ensuring smooth operations and timely baggage delivery.
- Transferring goods within distribution centers and warehouses, optimizing inventory management and logistics operations.
Weight-lifting machines
Weight-lifting machines are indispensable in the manufacturing industry, designed to manage heavy loads that are impractical or unsafe for human handling. These machines, such as overhead cranes and forklifts, are engineered to lift, lower, and transport heavy objects with precision and efficiency. Overhead cranes excel in lifting substantial materials in expansive industrial environments, while forklifts are commonly utilized in warehouses for efficient goods movement.
These machines are critical for ensuring operational safety and optimizing workflow efficiency within manufacturing facilities. They facilitate the handling of robust materials like steel components and machinery parts, significantly enhancing productivity.
Applications
- Maneuvering large automotive parts during assembly in automotive manufacturing plants, streamlining production processes.
- Managing heavy construction materials on job sites, supporting infrastructure development with reliable material handling solutions.
- Loading and unloading cargo in shipping yards, ensuring swift and efficient logistics operations.
- Transferring equipment within expansive manufacturing plants, facilitating seamless integration and operation across production lines.
- Supporting maintenance operations by safely lifting and moving machinery for repairs and upgrades.
Paper-cutting machines
Paper-cutting machines play a vital role in the manufacturing industry, particularly in sectors focused on paper products such as publishing and packaging. These machines encompass a spectrum from manual cutters to advanced automated systems, capable of precise cutting and managing large volumes of paper.
They employ sharp blades or laser technology to cut paper into specific shapes and sizes, essential for producing items ranging from books to packaging materials.
In manufacturing environments, paper-cutting machines are valued for their accuracy and consistency in production. They are indispensable for maintaining high standards of quality and operational efficiency, especially in industries where precise cutting is paramount.
Applications
- Cutting sheets for book publishing, ensuring precise trimming and sizing for various types of publications.
- Shaping cardboard into customized packaging designs, optimizing packaging solutions for diverse product needs.
- Trimming paper for printing industries, enhancing print quality and efficiency in commercial printing operations.
- Creating custom-sized paper products for specialized applications such as marketing materials and promotional items.
- Precision cutting for intricate paper crafts and artistic projects, supporting creativity in design and production.
Press brakes
Press brakes are pivotal machine tools extensively utilized in the manufacturing industry for bending sheet metal. They function by clamping the metal sheet between a punch and die, allowing for precise bends at specified angles and lengths. Available in hydraulic, mechanical, and servo-electric variants, each type offers distinct advantages in terms of accuracy, speed, and capacity.
These machines are indispensable in metalworking and fabrication industries, where they play a crucial role in producing metal components with exceptional precision. Their capability to create accurate bends makes them essential for manufacturing operations requiring precise metal parts.
Applications
- Fabricating intricate metal components for automotive assembly, ensuring durability and functionality in vehicle construction.
- Manufacturing casings and panels in the electronics industry, meeting stringent requirements for component protection and aesthetics.
- Constructing robust metal frames for structural applications in construction, providing strength and stability in building frameworks.
- Producing customized metal brackets and supports for industrial machinery, facilitating efficient operation and maintenance.
- Crafting architectural elements and fittings from metal, enhancing design flexibility and durability in building construction and renovation projects.
Quality testing machines
Quality testing machines are essential in the manufacturing process, pivotal for ensuring that products adhere to required standards and specifications. These machines encompass a wide spectrum, ranging from handheld devices to sophisticated automated systems. For example, coordinate measuring machines (CMMs) provide detailed 3D measurements of part geometry, while tensile testing machines assess the strength and elasticity of materials.
In manufacturing industries, these machines are critical for maintaining stringent quality control measures. They are utilized to rigorously test and validate the physical and mechanical properties of products, ensuring they meet safety, performance, and regulatory standards.
Applications
- Ensuring precise dimensional accuracy in automotive components, guaranteeing fit and functionality in vehicle assembly.
- Testing the strength and durability of construction materials, ensuring structural integrity and safety in building projects.
- Verifying the reliability and longevity of consumer electronics, meeting consumer expectations for product longevity and performance.
- Assessing the quality and consistency of pharmaceutical products, ensuring adherence to pharmaceutical regulations and standards.
- Monitoring the performance of aerospace components, ensuring reliability and safety in aviation and space applications.
Embroidery machines
Embroidery machines have transformed textile production in the manufacturing sector, offering unparalleled precision and efficiency in decorative stitching. These machines range from single-head units for small-scale operations to multi-head systems capable of executing intricate, large-scale designs. They function by using needles to apply thread or yarn onto a base material, creating detailed patterns and designs that are programmed using computer software.
In manufacturing environments, these machines are indispensable for embellishing garments and textiles with logos, decorative motifs, and personalized designs. They are essential in industries such as fashion, home décor, and branding, meeting the high demand for customized embroidery.
Applications
- Creating branded apparel for corporate uniforms, ensuring a professional and cohesive brand image.
- Producing elaborate embroidered designs on high-fashion garments, enhancing aesthetic appeal and exclusivity.
- Adding decorative elements to home textiles such as curtains, pillows, and tablecloths, enhancing interior décor.
- Customizing accessories like bags, hats, and footwear with unique embroidery, catering to individual preferences and trends.
- Embellishing promotional merchandise and gifts with personalized embroidery, enhancing brand visibility and customer engagement.
Shears
Shears in manufacturing are robust cutting tools essential for shaping and cutting materials such as metal, fabric, and plastic. Available in various types, from handheld shears for smaller tasks to hydraulic shears for cutting thicker materials, these tools are renowned for their precision and operational ease, featuring sharp blades capable of making clean, straight cuts.
In manufacturing facilities, shears are indispensable for their efficiency and accuracy in cutting operations. They play a pivotal role in industries requiring precise material shaping, including metal fabrication, textile production, and plastic manufacturing.
Applications
- Cutting and shaping sheet metal for automotive components, ensuring precision and durability in vehicle manufacturing.
- Trimming and tailoring fabrics in textile production, facilitating efficient garment manufacturing processes.
- Shaping plastic components for diverse applications, meeting stringent requirements for product design and functionality.
- Crafting intricate parts and components in metalworking, supporting the production of precise machinery and equipment.
- Performing maintenance tasks in industrial settings, providing quick and effective solutions for repairing and modifying materials.
Grinders
Grinders are indispensable tools in the manufacturing toolkit, utilized for cutting, grinding, and polishing materials with precision. They are available in various configurations, including angle grinders for handheld operations and bench grinders for stationary use. Grinding machines operate by employing abrasive grinding wheels to remove material, achieve smooth finishes, or reshape workpieces.
In the manufacturing sector, grinders play a crucial role in maintaining product quality and achieving precise outcomes. They find widespread application across diverse industries for tasks ranging from smoothing rough edges to preparing surfaces for finishing and shaping metal components.
Applications
- Smoothing and deburring edges in metal fabrication, ensuring safety and aesthetics in finished products.
- Preparing surfaces for painting or coating in automotive manufacturing, enhancing adhesion and durability of surface treatments.
- Sharpening cutting tools and equipment in machine shops, ensuring optimal performance and longevity of tools.
- Polishing finished metal products to achieve glossy finishes and enhance visual appeal in metalworking applications.
- Removing weld beads and excess material in metal fabrication, ensuring structural integrity and quality in welded components.
Overhead cranes
Overhead cranes are integral components in the spectrum of manufacturing equipment, particularly in environments where heavy lifting is routine. These cranes operate on rail systems, featuring a hoisting mechanism that traverses along a bridge.
Types of overhead cranes vary widely, including bridge cranes for expansive operations and gantry cranes for outdoor applications. These cranes are equipped with diverse lifting capacities and controls tailored to meet specific industrial needs.
In manufacturing industries, overhead cranes play a pivotal role in efficiently handling heavy and oversized loads, such as raw materials like steel and large machinery components. They are essential for enhancing operational efficiency and safety, significantly reducing risks associated with manual lifting tasks.
Applications
- Transporting and positioning raw materials within steel manufacturing plants, facilitating seamless production processes.
- Maneuvering large machinery components during heavy equipment manufacturing, ensuring precise assembly and installation.
- Loading and unloading heavy cargo in shipping yards, optimizing logistics operations for efficient goods movement.
- Assembling expansive structures in the construction industry, supporting construction projects with reliable lifting and positioning capabilities.
- Supporting maintenance operations in industrial facilities, providing critical lifting solutions for equipment servicing and repairs.
Surface treatment machines
Surface treatment machines are essential in the manufacturing industry for preparing, cleaning, and enhancing surfaces to meet specific requirements. These machines encompass a broad spectrum, ranging from sandblasting equipment for surface roughening to electroplating machines for applying protective coatings. The choice of machine depends on the desired outcome, whether it’s improving appearance, enhancing resistance to corrosion, or increasing surface hardness.
In industries where surface quality directly impacts product performance and aesthetics, these machines play a crucial role. They are extensively used in automotive, aerospace, and consumer goods manufacturing sectors.
Applications
- Electroplating metal components to enhance corrosion resistance and extend product lifespan in marine applications.
- Sandblasting surfaces to prepare them for paint adhesion and ensure durable finishes in automotive manufacturing.
- Polishing and finishing consumer goods such as jewelry and household appliances to enhance product aesthetics and appeal.
- Anodizing aluminum parts to improve surface hardness and durability for aerospace and electronic components.
- Etching surfaces for precise engraving and marking applications in industrial manufacturing and signage.
Boring machines and tools
Boring machines and tools are specialized equipment in manufacturing, designed for enlarging holes and achieving precise diameters in a variety of materials.
These machines range from manual hand-operated tools to advanced CNC (Computer Numerical Control) machines capable of performing high-precision operations. The selection of a boring machine depends on factors such as the material of the workpiece, its size, and the required level of precision.
In industries where the accuracy of hole dimensions is crucial, such as automotive, aerospace, and heavy machinery manufacturing, these machines are indispensable. They play a critical role in ensuring that components fit precisely and function as intended.
Applications
- Enlarging and refining holes in engine blocks for optimal performance and efficiency in automotive manufacturing.
- Performing precision boring operations in the manufacturing of aerospace components, meeting strict tolerances for aerospace applications.
- Creating precise holes in heavy machinery components to facilitate assembly and ensure operational reliability.
- Conducting customized boring operations in specialized manufacturing sectors such as renewable energy and medical device manufacturing.
- Refurbishing and re-boring worn-out parts in maintenance and repair operations, extending the lifespan of critical components in industrial settings.
Drilling machines and tools
Drilling machines and tools are indispensable equipment in manufacturing, used for creating holes in a variety of materials. These machines range from handheld drills to advanced CNC drilling machines. They operate by rotating a drill bit at high speed while applying pressure to penetrate the material and form holes. The choice of drilling machine depends on factors such as the material’s hardness, the size of the hole, and the required level of precision.
In manufacturing facilities, drilling machines are essential for a diverse range of applications, from creating intricate holes in electronic components to drilling large openings in construction materials. They are valued for their precision, efficiency, and versatility across different material types.
Applications
- Drilling precise holes in metal parts for machinery manufacturing, ensuring accurate assembly and operational functionality.
- Creating openings in construction materials such as concrete and steel beams for infrastructure projects, facilitating installation and structural reinforcement.
- Precision drilling in electronic component production, ensuring exact alignment and fit for circuit boards and microelectronics.
- Drilling holes in plastic materials for manufacturing consumer goods like appliances and toys, facilitating assembly and functionality.
- Machining holes in composite materials for aerospace and automotive industries, maintaining structural integrity and weight optimization in advanced applications.
Cutting machines and tools
- Cutting machines and tools are essential components in the diverse field of manufacturing, catering to various materials and precision requirements. These devices encompass a wide array, each designed for specific cutting needs:
- Laser cutting machines: Laser cutting machines use a high-powered laser beam to precisely cut materials. They are renowned for their accuracy and versatility in cutting a range of materials, including metals, plastics, and textiles. Types include CO2 lasers for general cutting and fiber lasers for efficient cutting of reflective metals.
- Oxy-Fuel cutting machines: Oxy-fuel cutting machines utilize a combination of oxygen and a fuel gas to cut through thick metals, particularly steel. They are valued for their capability to handle large-scale cutting tasks with high heat intensity.
- Plasma cutting machines: Plasma cutting machines employ ionized gas to cut through electrically conductive materials like steel, aluminum, and copper. They are known for their speed and efficiency in industrial cutting applications.
- Waterjet cutting machines: Waterjet cutting machines use a high-pressure stream of water mixed with abrasive particles to cut a wide variety of materials, including metals, composites, and stone. They offer precision and versatility without heat-affected zones.
In manufacturing industries, cutting machines and tools play pivotal roles across various applications:
Applications
Precision cutting of intricate designs in metal for automotive parts, ensuring exact specifications and quality in production.
Creating fine patterns and precise cuts in electronics manufacturing for components such as circuit boards and semiconductor materials.
Cutting and shaping textiles with intricate patterns and designs for fashion and interior decor industries, ensuring high-quality finished products.
Producing complex components with tight tolerances for aerospace applications, ensuring structural integrity and performance in critical parts.
Drill press
A drill press is a stationary drilling machine renowned for its precise control and accuracy, surpassing handheld models.
It comprises a base, column, table, spindle, and drill head, typically powered by an electric motor. Drill presses are available in various configurations, including benchtop and floor-standing models, tailored to different manufacturing needs.
The primary advantage of a drill press lies in its ability to consistently produce clean, accurate holes with precise depth and angle control.
Applications
In manufacturing environments, drill presses find diverse applications across industries:
- Automotive manufacturing: Used for creating precise holes in metal components such as engine parts and chassis components, ensuring accurate assembly and functionality.
- Woodworking: Essential in furniture making and carpentry, providing precise drilling capabilities for creating joints, holes, and intricate designs in wood.
- Aerospace manufacturing: Employed for crafting critical components like aircraft fuselage panels and structural elements, meeting stringent aerospace standards for precision and reliability.
- Electronic assemblies: Used in electronics manufacturing for precision drilling of circuit boards and assembly components, ensuring exact alignment and functionality.
Milling machines, among the more substantial investments in industrial machine tools, are indispensable in the manufacturing sector for shaping and cutting materials, particularly metals. These machines operate by rotating a cutting tool against the workpiece, allowing for precise material removal.
They come in various types, such as horizontal and vertical milling machines, each offering distinct capabilities based on the orientation of the cutting tool and the type of milling operation required.
Applications
In manufacturing environments, milling machines are integral across diverse applications:
Machinery Production: Used for shaping metal parts like gears, shafts, and housings, ensuring precise dimensions and smooth surfaces in heavy machinery and equipment manufacturing.
Aerospace Industry: Essential for fabricating complex components such as aircraft wings, fuselage structures, and engine parts, meeting stringent aerospace quality and performance standards.
Automotive Parts Manufacturing: Employed for milling slots, threads, and intricate features in engine blocks, transmission components, and chassis parts, ensuring precision and reliability in automotive production.
Electronics Industry: Utilized for precision milling of circuit boards and electronic components, enabling the creation of intricate patterns and precise mounting surfaces in electronic assemblies.
Turning machines and tools
Turning machines, commonly referred to as lathes, are pivotal in manufacturing for shaping materials, particularly metals, by rotating the workpiece against a cutting tool.
These machines encompass a range of types, from traditional manual lathes to sophisticated CNC (Computer Numerical Control) lathes, each tailored to specific manufacturing requirements.
Turning machines are renowned for their ability to produce symmetrical components with precision and efficiency.
Applications
In industrial settings, turning machines play crucial roles across diverse applications:
- Automotive Industries: Used extensively for manufacturing cylindrical components such as axles, crankshafts, and brake discs, ensuring precision fit and functionality in vehicle assembly.
- Aerospace Manufacturing: Essential for producing precision parts like turbine shafts, landing gear components, and aerospace structural elements, meeting stringent aerospace quality and safety standards.
- Defense Equipment Production: Employed for crafting critical components for military vehicles, weapons systems, and defense electronics, ensuring reliability and performance in defense applications.
- General Metal Fabrication: Utilized for turning operations in various metalworking processes, including creating shafts, bushings, and fittings for diverse industrial applications.
Swiss turning machine
Swiss turning machines, and specialized lathes, are esteemed for their precision in crafting intricate parts. These machines excel in producing small, complex components crucial to industries like watchmaking, medical technology, and electronics. They feature a unique sliding headstock design that positions the workpiece close to the cutting tool, minimizing deflection and ensuring exceptional accuracy.
Applications
- Crafting miniature components for high-precision surgical instruments
- Manufacturing intricate gears and mechanisms for luxury timepieces
- Producing micro-sized connectors and electronic components
- Precision turning operations essential for advanced micro-machining techniques
Lathe
The lathe stands as one of the most versatile and indispensable machines in manufacturing, capable of executing a variety of operations such as cutting, sanding, knurling, and drilling. Lathes are essential for creating symmetrical products by rotating the workpiece around an axis. They are available in several types, including engine lathes, turret lathes, and CNC lathes, each designed to fulfill specific manufacturing needs and offering distinct functionalities.
Applications
In industrial applications, lathes serve critical roles across a wide spectrum:
- Automotive manufacturing: Used extensively for shaping metal parts like shafts, bushings, and engine components, ensuring precision and durability in automotive assemblies.
- Industrial machinery: Essential for producing cylindrical components such as gears, pulleys, and bearings used in heavy machinery and equipment manufacturing.
- Woodworking: Employed for crafting decorative elements like table legs, spindles, and handles, providing intricate designs and smooth finishes in furniture and cabinetry production.
- Metal fabrication workshops: Utilized for various turning operations, including creating threaded parts, flanges, and fittings essential in metalworking processes for structural and functional components.
EDM machine
Electrical Discharge Machining (EDM), a pivotal tool in the manufacturing industry, is renowned for its capability to machine complex shapes and hard materials that pose challenges for conventional machining methods. EDM operates by utilizing electrical discharges or sparks to shape a workpiece through controlled erosion. There are primarily two types of EDM machines: wire EDM, employing a thin wire for cutting, and die-sink EDM, which uses a shaped electrode to create impressions.
Applications
In industrial applications, EDM machines play critical roles across various sectors:
- Toolmaking: Essential for crafting intricate molds and dies used in injection molding, die casting, and precision tooling applications, ensuring high dimensional accuracy and surface finish.
- Aerospace industry: Used extensively for producing aerospace components with intricate geometries, such as turbine blades, engine components, and aircraft structural parts, where precision and durability are paramount.
- Medical device manufacturing: Crucial for manufacturing precision parts like surgical instruments, implants, and medical device components requiring complex shapes and high-quality surface finishes for medical applications.
- Automotive sector: Applied for creating detailed patterns and molds used in automotive manufacturing, including components like gears, engine parts, and transmission systems, where accuracy and reliability are crucial for performance and safety.
ECM machine
Electrochemical Machining (ECM) stands out in the manufacturing equipment landscape as a method for shaping metal workpieces through controlled anodic dissolution. ECM excels in machining complex shapes in difficult-to-machine materials with exceptional precision, all without introducing stress or heat-affected zones. Types of ECM machines include jet-type ECM, ideal for intricate features, and cavity-type ECM, suited for larger surface areas.
Applications
- Aero-engine components: Used extensively to generate intricate shapes in critical components like turbine blades and engine casings, where precision and durability are essential for aerospace performance.
- Defense sector: Employed for machining high-precision parts such as weapon components and specialized equipment, ensuring stringent specifications and operational reliability.
- Turbine blade manufacturing: Essential for producing turbine blades with intricate features and optimal aerodynamic profiles, crucial for efficiency and performance in power generation and aerospace applications.
- Medical implants: Utilized in fabricating medical implants with smooth surface finishes and precise geometries, ensuring biocompatibility and long-term functionality in healthcare applications.
EBM machine
Electron Beam Machining (EBM) represents a cutting-edge technology in manufacturing, utilizing a focused beam of high-velocity electrons to precisely remove material from workpieces. Renowned for its capability to achieve intricate details, EBM is particularly advantageous for processing high-strength materials that pose challenges to conventional machining methods.
Applications
- Fabricating nanoscale components for semiconductor devices
- Machining titanium and other tough alloys for aerospace applications
- Creating delicate surgical instruments and implants for medical use
- Engineering specialized cutting tools for precision manufacturing
Machining centers
Machining centers are pivotal in the manufacturing equipment realm, celebrated for their unparalleled versatility and precision. These sophisticated machines integrate multiple functions such as drilling, milling, and tapping into cohesive systems, significantly enhancing operational efficiency. Available in diverse configurations, each tailored to specific manufacturing needs, machining centers play a crucial role in meeting dynamic market demands.
Horizontal machining centers
Horizontal machining centers feature a spindle oriented horizontally, distinguishing them from vertical counterparts. These machines excel in precision applications and offer distinct advantages in chip evacuation, making them ideal for projects requiring intricate machining from multiple angles.
Applications
- High-speed production of automotive engine components
- Precision milling for aerospace structural parts
- Complex machining tasks in heavy industrial equipment fabrication
- Manufacturing critical components for defense systems
Vertical machining centers
Vertical machining centers utilize a vertically oriented spindle, simplifying setups and often costing less than horizontal models. They are prized for their versatility and are favored for a wide array of applications across various industries.
Applications
- Manufacturing housings and components for consumer electronics
- Producing medical implants and surgical instruments
- Crafting intricate molds and dies for tooling applications
- General machining operations in small to medium-sized manufacturing facilities
Advantages of using industrial machines in the manufacturing industry
The manufacturing industry has undergone a remarkable transformation, driven by the integration of advanced industrial machines and equipment.
These innovations have not only enhanced traditional manufacturing processes but also opened up new avenues for efficiency, cost-effectiveness, quality assurance, and operational safety.
- Increased Efficiency: Industrial automation, exemplified by CNC milling machines and robotic assembly lines, has revolutionized task execution, significantly reducing lead times. Technologies like conveyor belts and automated sorting systems minimize manual intervention, thereby optimizing overall operational efficiency.
- Cost Savings: The adoption of advanced manufacturing equipment, including energy-efficient machines, translates into substantial savings in energy and operational expenditures. Automation decreases reliance on labor-intensive processes, leading to significant reductions in labor costs.
- Consistency and Quality: Precision tools such as lathes and laser cutters ensure consistent high-quality output. Automated inspection systems guarantee that every product meets stringent quality standards, bolstering reliability and customer satisfaction.
- Safety: Modern machinery incorporates advanced safety features that mitigate workplace hazards. Robots and automated systems handle hazardous materials safely, minimizing risks to human workers and promoting a secure work environment.
- Flexibility: Versatile machines can be programmed and reconfigured to perform various tasks, enabling manufacturers to swiftly adapt to changing market dynamics. Technologies like CNC machining and 3D printing facilitate customizable production, meeting diverse customer requirements efficiently.
- 24/7 Operation: Automated systems operate continuously, maximizing output and meeting round-the-clock production demands, thereby enhancing overall productivity.
- Environmental Sustainability: Many modern machines are designed with sustainability in mind, reducing waste and minimizing environmental impact through efficient resource utilization and eco-friendly practices.
- Enhanced Supply Chain Management: Sophisticated equipment such as RFID tracking and automated storage systems optimize supply chain operations, enhancing inventory management efficiency and responsiveness to market demands.
- Scalability: Advanced manufacturing equipment empowers businesses to scale operations seamlessly in response to market fluctuations, ensuring agility and competitiveness in dynamic business environments.
Conclusion
Manufacturing machinery is the cornerstone of modern industry. With the information sheets we provide, you can choose the equipment according to your production needs.