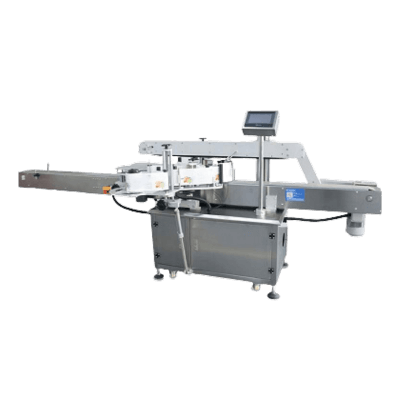
Front and back labeling machine
The BGJ-S350 is the flawless solution for precise labeling of square products, whether you need double-sided application like front and back labeling. Its features offer:
Applications of front and back labelers
These machines are particularly well-suited for applying labels to both the front and back of containers such as bottles, jugs, tubs, and a variety of square, rectangular, and oval containers. They can efficiently label containers made from glass, plastic, metal, and paper.
Here are some applications:
Why choose the front and back labeling machine at LMS
The LMS front and back labeling machine is versatile, and suitable for both double-sided and single-sided labeling across various industries, including food, chemicals, and electronics.
Designed for labeling flat and square items, it features a compact, robust structure with a minimal footprint. This machine is equipped with positioning devices and fault alarms.
Our skilled after-sales team offers one-year maintenance and training services, making us a trusted partner for countless manufacturers worldwide!
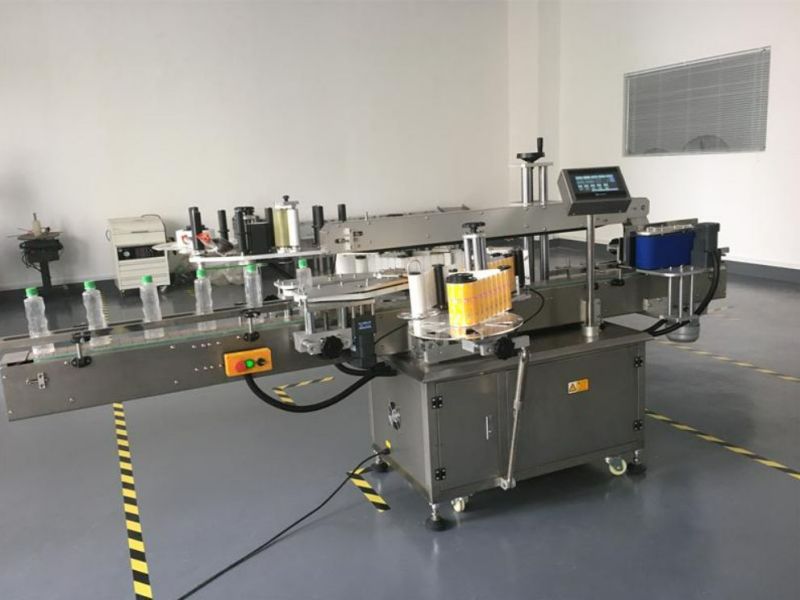
What is a front and back labeler?
A front and back labeler is a type of packaging machine designed to apply labels to both the front and back sides of products simultaneously.
It is commonly used for bottles, jars, and other cylindrical items, ensuring accurate and consistent label placement for branding and regulatory compliance in various industries.
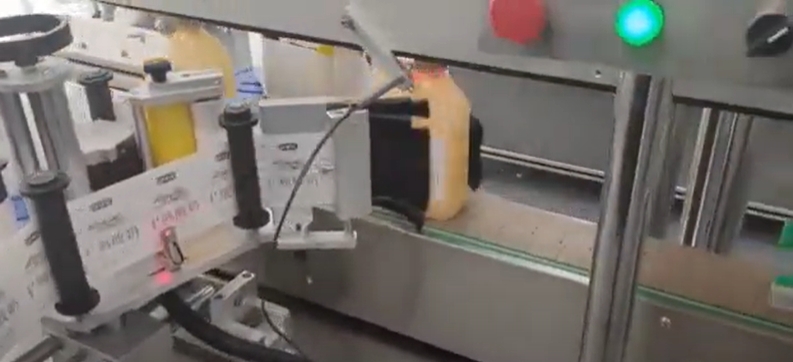
Customize services
We create a front and back labeler tailored precisely to your specifications. Here’s our approach:
Talk and Plan: We start by having a conversation with you to fully grasp your needs. With your input, we draft a design for a machine that does exactly what you envision.
Build: Once the design is finalized and approved by you, we begin assembling it using only the finest components.
Test and Check: You’ll have the opportunity to see your machine in action at our facility. This is the moment when you can confirm its perfection or suggest any adjustments.
Setup and Support: We assist with the installation at your location and ensure everything operates flawlessly. We also handle any necessary documentation to get you up and running.
Customization always takes into account the product’s dimensions, label size, labeling position, and specific needs to suggest the best-suited model for you. Optional features include:
- Integration with the production line for automated feeding.
- In-line printing capabilities for things like batch numbers.
- Detection and removal of missed labels.
- Automated collection post-labeling.
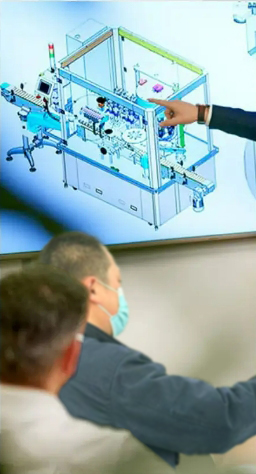
Front and back labeler FAQs
- How do front and rear labeling machines ensure label alignment accuracy?
Most of the top & bottom labelers are designed with easy-to-adjust mechanical structure, which allows users to adjust the position and angle of the labeling head according to different product sizes to ensure accurate labeling.
- What safety procedures are required for front and back labeling machines?
All safety guidelines should be followed when operating front and rear labelers, including but not limited to wearing proper protective equipment, regularly checking safety devices, and following the manufacturer’s operating manual.
- Can our facility receive a custom design tailored to its layout?
Certainly! Our engineering team will gladly create a specific design for your facility’s layout at no extra cost before we provide a final quote.
- What is the expected delivery time for our machine after placing an order?
The delivery period can vary depending on the particular model and our current production line. Typically, it falls between 6 to 8 weeks.
- How long will it take to receive our machine after placing an order?
Delivery duration for your machine will depend on the model chosen and our current production schedule, but it generally takes between 6 to 8 weeks.
- What kinds of payment methods are accepted?
We support a variety of payment options to match your needs, including wire transfers, credit card transactions, and PayPal.
- What kind of after-sales service is provided?
We are dedicated to supporting your equipment for its entire operational lifetime. This includes offering ongoing online support, ensuring parts are available when needed, and conducting regular maintenance to keep the machine running smoothly.
- Is training provided for the operation and maintenance of the machine?
Yes, we provide free online training to help you acquire the skills and knowledge necessary for efficiently operating and maintaining your machine.
- What is included in the warranty for our machines?
Our machines come with a standard one-year warranty, which you can choose to extend to ensure continued coverage and peace of mind.