Various types of labeling machine, as their designation suggests, are instruments dedicated to affixing or enveloping labels (presented in rolls or substantial quantities) onto the exteriors of products or containers such as bottles, bags, boxes, etc.
Beyond merely dispensing or attaching labels, some of these machines are also equipped with the capability to print them, offering a versatile solution to labeling needs.
The market is flooded with an extensive array of labeling machines, spanning from highly automated units that facilitate seamless integration of the printing and application processes to manual devices that allow for straightforward label dispensing.
Engineered to cater to a diverse spectrum of items or products, certain labeling machines are meticulously designed for specific applications, whereas others boast versatility and are compatible with a wide variety of packages, containers, and products.
The current market is saturated with numerous models, conceived and constructed by a wide range of manufacturers. This variety ensures that, for almost any conceivable labeling requirement, there is a machine perfectly suited to the task at hand.
With such a plethora of options, selecting the ideal labeling machine for any given application becomes a feasible endeavor.
The text primarily focuses on the various categories of labeling machines.
Given the diversity in labeling subjects and the unique contours of label materials, labeling demands vary significantly. As such, to accommodate the diverse labeling requirements presented by different scenarios, labeling machines come in a multitude of types and models.
The exposition on labeling machines in this document is structured around several key dimensions:
- Based on automation levels
- Based on labeling capabilities
- Based on label varieties
- Based on container movement
- Based on equipment movement
- Based on automation levels
Based on automation levels: Label machines are categorized into hand-operated, semi-automated, and fully automated models. When delving into the world of label applicators, one discovers that manufacturers present a variety of options influenced by cost, container compatibility, operational speeds, and setups, among others.
Acquiring knowledge about these variations is crucial before finalizing a purchase to ensure a choice that aligns with your needs. Here’s a condensed guide to the prevalent types of label applicators, organized from those suitable for modest to extensive volume labeling tasks.
This assortment ensures that regardless of the scale or specifics of your labeling requirements, you have the necessary information to select an appropriate solution.
Hand-operated label machine
For individuals aiming to upgrade from manual sticker placement without investing heavily in label application machinery, a hand-driven label applicator emerges as a budget-friendly choice.
These manual machines are capable of affixing up to a thousand labels per hour onto cylindrical objects ranging from 1.5” to 5” in diameter. Their affordability is matched by the convenience of quick setup and the basic training requirements they entail.
This cost-efficient manual labeling device is adept at handling cylindrical containers such as bottles or jars, whether made of glass or plastic, and can also serve as a hand-operated can labeling tool.
Semi-automated label machine
Operable through a foot pedal or a manual switch, semi-automated label machines represent a significant advancement from manual label applicators. These machines, more efficient than their manual counterparts, often come with the ease of activation via a simple switch mechanism.
Compact in design, they are versatile enough to accommodate the labeling of various container types across multiple sides, including both the front and back. The investment in a semi-automated labeling machine can quickly become cost-effective by enhancing labeling speed to align with the pace of production.
Termed as semi-automated units, these machines are powered by electronic systems designed to apply self-adhesive labels across a diverse array of products and packaging types. They are particularly adept at handling smaller production volumes and specific batch numbers, offering an optimal solution for such requirements.
In contrast to fully automated label applicators, the semi-automated systems require operator intervention to start the labeling process. The operator manually places the product inside the machine and initiates the labeling with a few simple actions. After the application, the product is then removed manually. This level of involvement ensures precision and adaptability for short runs or special labeling tasks.
Semi-automatic flag labeling machine
Semi-automatic labeling machines necessitate human operation to function effectively, as suggested by their designation. LMS presents its unique product, the Semi-auto Flag Labeling Machine, tailor-made for smaller enterprises or individual operations. These semi-automatic systems, governed by electronic controls, excel in affixing labels to an expansive spectrum of products and packaging, utilizing various self-adhesive label types.
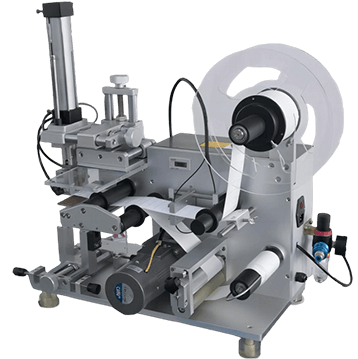
The Semi-auto Flag Labeling Machine by LMS stands out for its adaptability, capable of processing a diverse array of materials. This includes round wires, flat wires, round tubes, flag-shaped items, lollipops, flower branches, and even optical cables. This versatility makes it an invaluable asset for businesses or hobbyists dealing with unique labeling needs or a variety of product types.
Designed with ease of use in mind, this machine bridges the gap between manual labeling efforts and the need for higher efficiency without the full leap to automation. It’s an ideal solution for those looking to increase their labeling capacity and precision while managing a range of different items, all within the realm of semi-automated technology
Fully automatic labeling machine
Scaling operations often necessitate the transition from manual or semi-automatic solutions to fully automatic labeling systems to cater to large-scale labeling tasks. A fully automatic labeling machine represents a significant leap in automation, providing essential benefits for projects demanding high-volume output.
These machines are a more substantial financial commitment but offer advantages in terms of packaging uniformity and accelerated production rates. Utilizing automatic labeling machinery for bulk quantities significantly reduces the labor cost per unit compared to semi-automatic alternatives.
Fully automatic labeling devices are designed for seamless integration into virtually any existing packaging line, ensuring bottles and other containers are labeled with precision and speed as they move along powered conveyors.
Moreover, manufacturers can produce custom labeling machines tailored for specific or unconventional labeling needs. To enhance the functionality of these automatic systems, a range of accessories is available, including coders that enable direct printing on labels or the containers themselves, further streamlining the labeling process and boosting efficiency.
Based on labeling capabilities
Based on labeling capabilities: Label applicators are categorized into models designed for top surface labeling, side labeling, corner application, and encircling label placement.
Flat labeling machine
The flat labeling machine excels in applying labels to the top surfaces of various packaging forms, such as lids, caps, boxes, cartons, and bags, finding its application across numerous sectors including pharmaceuticals, cosmetics, chemicals, food and beverages, pesticides, gifts, agriculture, and electronics.
This machine stands out for its versatility, enabling the labeling of a broad spectrum of items. A single unit can meet virtually all flat surface labeling needs, making it particularly beneficial for operations with low volumes, diverse products, and frequently changing specifications. This adaptability significantly enhances labeling efficiency while minimizing the need for multiple pieces of equipment, thereby reducing investment costs.
LMS presents both the automatic plastic bag labeling machine and the automatic vacuum pouch labeling machine; your choice largely hinges on the need for efficiency, precision, and bubble elimination.
Automatic plastic bag labeling machine
The automatic plastic bag labeling machine is a cutting-edge solution designed to enhance the efficiency and accuracy of the labeling process. This machine surpasses traditional manual labeling methods in speed, thereby significantly boosting productivity. It is meticulously engineered for the automatic sorting, labeling, and collecting of a wide array of card-based products.
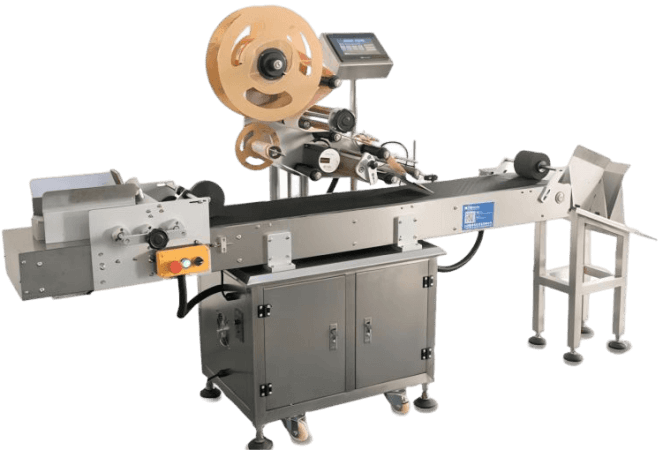
Utilizing sophisticated flexible card separation technology, it ensures a smooth and flawless separation of cards, eliminating any risk of damaging the products. Its versatility extends to an assortment of items, including scratch cards, unassembled paper boxes, PE bags, paper bags, magazine covers, and color pages, among others.
Furthermore, this machine showcases its adaptability by doubling as a tool for applying protective films to various plastic surfaces, guaranteeing high precision and a bubble-free application, making it an indispensable asset for any operation looking to streamline its labeling or protective film application processes.
Automatic vacuum pouch labeling machine
The automatic vacuum pouch labeling machine revolutionizes the labeling process for soft packaging materials like bags, integrating an advanced suction cup mechanism for seamless pickup and placement of bags onto the conveyor for labeling.
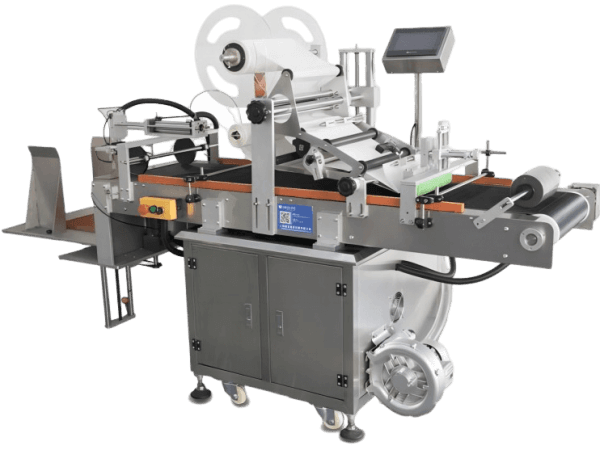
This system, a product of meticulous research and design by our team, encompasses sophisticated components for paging, labeling, paper collection, sensing, and transmission. It stands out for its ability to automatically detect and apply labels with high precision and aesthetic appeal, ensuring labels are perfectly aligned and presented.
Moreover, this innovative machine boasts a highly accurate product weight recognition feature, minimizing errors significantly. Tailored customization options are available to perfectly align with specific operational requirements, making it a versatile solution for businesses seeking to optimize their labeling process for vacuum pouches and similar soft packaging materials.
Top label applicator
The Top adhesive labeling machine, often referred to as a top label applicator or labeler, serves a pivotal role in affixing labels to the upper surfaces of a variety of products.
This machinery finds its application across several key industries including food and beverage, cosmetics, and pharmaceuticals, where the precision and reliability of labeling are paramount for the sake of product identification and traceability.
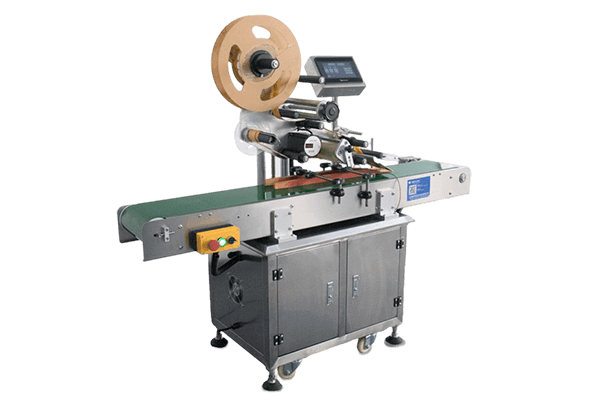
This fully automated machine is specifically engineered for the application of labels or adhesive films to flat surfaces, accommodating a range of items such as books, folders, boxes, and paper bags.
Its versatile labeling mechanism is adaptable, allowing for the labeling of items with uneven surfaces, making it an ideal solution for extensive flat labeling requirements and objects possessing substantial flat areas.
Further enhancing its utility, this machine can be outfitted with a coder or inkjet printer, enabling the direct printing of essential data like production dates, batch numbers, barcodes, and additional pertinent information directly onto the labels, thereby ensuring a comprehensive labeling solution.
Side labeling equipment
The side labeling equipment adeptly performs labeling or film application on the lateral planes and curved edges of items, including cosmetic bottles and square packages. This machine’s capability extends to applying labels on one or multiple sides, crucial for displaying variable data like expiration dates, batch numbers, or components on products ranging from food packaging to cosmetics, household items, glass, and plastic containers or cardboard boxes.
Regardless of the shape—be it flat folding boxes, cubic parcels, or oval containers, often utilized for bottles—the aesthetic appeal and seamless label application are vital for attracting customers at the point of purchase. Our labeling systems offer the versatility needed and are globally recognized across various sectors.
Designed for high-velocity production environments, our dual-sided sticker labeling machines excel in applying adhesive labels simultaneously to both sides of a product, boosting operational efficiency and offering diverse labeling solutions to meet the demands of different industries.
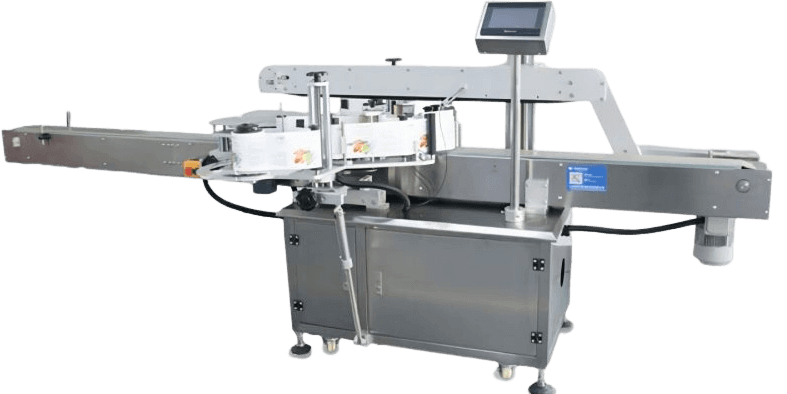
Automated bi-directional label applicator
The bi-directional label applicator is ideally suited for a variety of sectors, including food, beauty, medicine, and pesticide, among others. It offers both single and dual-side labeling capabilities for a range of bottle shapes, including flat, cubical, and cylindrical.
Edge Labeling machine
Edge labeling machines are crafted to attach labels across two joining sides to ensure product integrity. These machines specialize in edge labeling for boxes, targeting both the flat top and adjacent side surfaces to offer tamper-proof functionality. Their primary application includes securing products like playing cards, electronics packaging, and pharmaceutical boxes against tampering.
The edge labeling machine is tailored to meet the packaging industry’s demands for reliable product information and security tags, addressing safety concerns throughout the logistics and supply chain sectors. With a labeling capability of 30 to 60 items per minute and an accuracy of ±1 mm, this automatic edge labeling solution can integrate seamlessly with flat labeling systems for efficient, uninterrupted labeling operations.
Automated box edge labeling machine
Designed exclusively for corner labeling, this system targets the junction of the top and side planes of boxes, serving as a deterrent against unauthorized opening.
Its primary function is in affixing tamper-evident labels to products such as card packs, electronic gadgets, facial mask packaging, and pharmaceutical containers, ensuring a dual-sided labeling approach.
The automated edge labeling mechanism seamlessly integrates with additional labeling equipment, enhancing the security and integrity of packaging across various industries.
Circumferential Labeling machine
The circumferential labeling system employs a technique where labels are rolled onto the surface of a container, offering a straightforward alternative to more complex labeling methods, akin to the effect of shrink-wrapping.
Predominantly favored for cylindrical bottles, these labels are versatile enough to adhere to various materials including plastic, glass, metal, and cardboard, making them suitable for nearly any type of container.
This method encircles the container with the label, effectively utilizing the available surface area for maximum branding and information dissemination. Particularly in the beverage industry, it facilitates the consolidation of essential brand details and compliance with UPC standards on a single label.
Circumferential labeling stands out for its ability to fully or partially envelop the product in a label along its outer curve, thus maximizing label visibility. This is especially critical as industries face increasing legal obligations regarding product labeling, necessitating the optimal use of space on the product for information display.
Vertical round bottle labeling machine
The vertical round bottle labeling machine is engineered to optimize labeling operations, streamlining the process with automation for efficiency and simplicity. It ensures rapid labeling speeds while maintaining uniformity and aesthetic appeal in the placement of labels, making it an ideal choice for round containers across sectors like pharmaceuticals, food and beverage, cosmetics, and household chemicals.
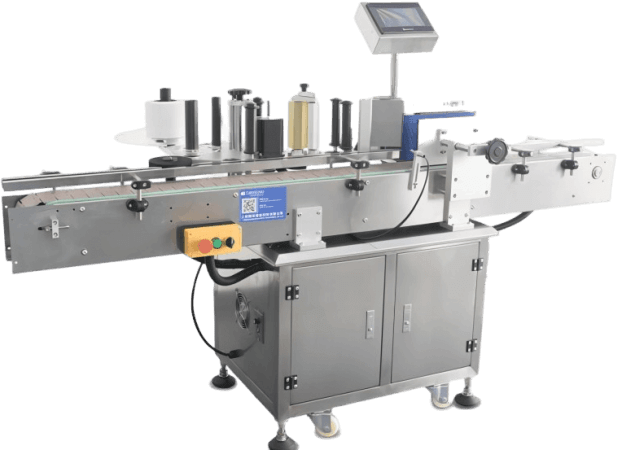
This machine is adept at handling an extensive array of container dimensions and forms, supporting diverse label mediums such as paper, vinyl, and plastic. Its versatility and reliability make it a vital asset for businesses looking to enhance their labeling processes with precision and consistency.
Based on label varieties
Categorization by label type sees labeling machines classified into four main types: wet glue labeling machines, self-adhesive (pressure sensitive) labeling machines, hot melt glue labeling machines, and shrink sleeve labeling machines. This division isn’t about the label material itself, but rather focuses on the method by which the label is affixed to the product.
Each category offers unique application techniques, tailored for specific labeling requirements and product types, ensuring that labels are applied efficiently and securely, regardless of the container’s material or shape.
Wet glue labeling machine
This machine is designed for the application of paper labels using wet glue, catering to a wide array of cylindrical containers such as bottles, jars, and cans made from glass or plastic. It operates by applying labels from a stack, using a glue that remains fluid at ambient temperatures, to affix labels onto rigid containers at impressive speeds, making it an ideal choice for labeling beer, spirits, and other beverages.
Especially adept for use in moist conditions typical of liquid beverage filling lines, wet glue labeling remains a preferred method for its efficiency and the high-quality application it offers.
The labels, often intricate with embossed designs and cut into unique shapes, can adhere to various container forms, enhancing the product’s visual appeal. This machine’s capability to apply multiple labels to a single container allows for a versatile labeling process, accommodating complex packaging designs.
Cold glue labeling machine
Introduction: The cold glue labeling machine is adept at applying labels to cylindrical containers, ensuring compatibility across a diverse range of round bottle types.
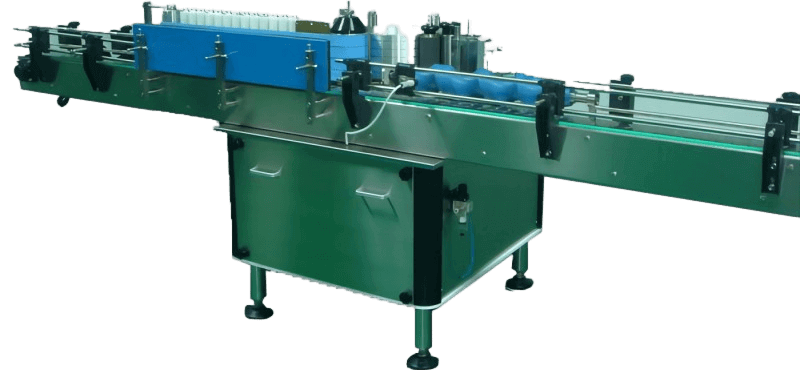
Its application extends to various industries, including food production, canning, distilleries, general chemical manufacturing, and pharmaceutical fields, marking its versatility and widespread utility.
This machine stands out for its economical operation and straightforward handling, boasting stable performance that results in smooth, aesthetically pleasing labeled products.
It is specially engineered to handle the demands of applying cold glue labels, making it an essential piece of equipment for businesses seeking efficient and reliable labeling solutions for their round container products.
Self-adhesive labeling machine
Self-adhesive labeling machines apply labels that come pre-glued on rolls of backing paper or film, eliminating the need for water or heat to activate the adhesive.
This technology has become a preferred choice, overtaking traditional wet glue methods, thanks to its versatility and the convenience of a no-mess application process.
The labels, which can be crafted from a variety of materials, not limited to paper, are die-cut into intricate shapes and stored on the roll, ready for application with minimal risk of damage.
This labeling approach is especially suited for a broad range of applications, from soft packaging to rigid containers, without risking damage to the product from water or heat. Pressure-sensitive labels, with their ready-to-stick adhesive backing, adhere to nearly any surface upon the application of light to moderate pressure.
The machine seamlessly feeds customized labels from the rolls, guiding them through to an applicator grid and onto the product using a vacuum applicator grid. At this critical point, the machine applies just enough pressure to activate the adhesive, securely attaching the label to the product at medium to high speeds.
Hot melt adhesive labeling machine
This machine utilizes adhesives that are solid at room temperature, transitioning to liquid form when heated for label application.
As an advanced iteration of traditional wet glue labeling methods, hot melt label applicators adapt by heating various adhesives to a liquid state before application, contingent on the specific needs of the product, packaging material, or ambient conditions within the packaging facility.
Such machines are particularly adept at applying wrap-around labels, covering extensive portions of a container’s body and surface.
In this precise application process, containers first receive adhesive from dispensing nozzles before reaching the label dispenser, while they are held stationary on rotary plates.
This method enables exceptionally accurate adhesive applications. The containers are then rotated in the opposite direction of the labeler carousel, ensuring the wrap-around labels are detached cleanly from the dispenser, preventing glue buildup on adjacent labels which could compromise the labeling process.
Linear-type OPP hot glue labeling machine
Embracing state-of-the-art processing and software control technology, our linear-type OPP labeling machine is tailored for the high-speed application of labels on a variety of round containers.
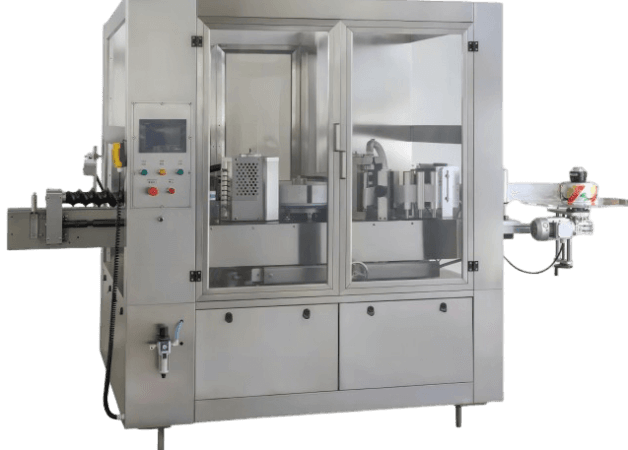
This machine is specifically designed to handle both empty and filled bottles, showcasing its flexibility and efficiency. It seamlessly accommodates (OPP/BOPP) labels, making it ideal for a broad spectrum of products including plastic bottles, cans, and barrels.
The machine’s adaptability and performance make it a perfect solution for industries involved in water, beverages, and other liquid products, ensuring a smooth and efficient labeling process that meets the demands of high-volume production environments.
Shrink sleeve labeling machine
This device encapsulates rigid containers by sliding a sleeve of either plain or printed thermoplastic material over the container’s neck or body and then applying heat to shrink the sleeve precisely to the container’s shape.
Designed to envelop the entire surface of the container, these sleeves offer both a full-body label and a measure of tamper-proof security. They are ideally suited for uniquely shaped containers across industries such as beverages, beauty products, and personal care items.
Operating with remarkable efficiency, the machine dispenses heat-shrinkable sleeves from rolls, where the sleeves are pre-printed with branding and product information.
The innovative mechanism of this device seamlessly transforms the flat sleeve into a cylindrical shape around the container, cutting it to the perfect length before shrinking it, all at an impressive pace.
The process involves two primary steps: firstly, positioning the plastic sleeve over the moving bottle on a conveyor; secondly, passing the sleeved bottle through a heat tunnel, which tightly conforms the sleeve to the bottle with a smooth, wrinkle-free finish. The heat tunnel is calibrated to deliver the precise heat intensity and duration needed to achieve the desired label fit.
Based on container movement
Labeling machines are differentiated by the movement direction of the container they’re designed to handle, and categorized into vertical and horizontal labeling machines. This distinction is particularly relevant for the labeling of cylindrical items. The choice between the two machine types hinges on the container’s stability and orientation during the labeling process.
Vertical labeling machines are best suited for containers that are stable on their feet and can move upright along the conveyor belt, such as food jars, cosmetic bottles, and pesticide containers. On the other hand, horizontal labeling machines cater to containers that lack stability or cannot stand upright during the labeling process, including pharmaceutical vials, ampoules, and syringes.
Vertical Labeling Machines: Here, containers proceed in an upright position through the machine, making it an ideal solution for bottles with a minimal taper or those that are square or rectangular. These machines are capable of applying both partial and full labels efficiently.
Horizontal Labeling Machines: In this setup, containers move lying on their sides, which is particularly advantageous for labeling round containers that are prone to tipping over, such as vials and bottles with rounded bottoms. This approach ensures a stable and effective labeling process for otherwise unstable containers.
*These two labeling machines only exist in the classification of self-adhesive labeling machines.
Based on equipment movement
Labeling machines are classified based on the movement path of the equipment, splitting into two primary types: inline labeling machines and rotary labeling machines. This distinction primarily lies in how bottles are handled during the labeling process. In an inline labeling machine, bottles remain on a conveyor belt throughout the application of labels.
Conversely, a rotary labeling machine involves transferring bottles onto a rotating turret for label application. Here, each bottle is securely held by a plate at the base and a centering device at the top, allowing for 360-degree rotation to precisely position the bottle for label application.
The diameter of the turret varies according to the speed requirements and the number of labeling stations incorporated into the machine. The rotary design’s compact footprint allows for multiple labeling stations, offering an advantage over the more spread-out inline labelers.
A significant distinction between the two types also involves the bottle change mechanism: inline labelers typically adjust for different container sizes with mechanical modifications such as sliding rails and height adjustments.
Rotary labelers, however, utilize specific change parts for different bottle sizes, including infeed and outfeed star wheels and guide rails, to facilitate smooth transitions between bottle types.
Conclusion
The diverse types of labeling machine available today are designed to meet the varied needs of different industries, accommodating a wide range of products, containers, and labeling requirements.
From hand-operated to fully automated systems, these machines offer solutions tailored to the specific demands of labeling tasks, whether they involve applying labels to flat surfaces, wrapping them around cylindrical bottles, or securing them to uniquely shaped containers for tamper evidence.
The choice between vertical, horizontal, inline, or rotary machines hinges on the physical characteristics of the container and the operational context, highlighting the importance of selecting the right type of labeling machine.
With this comprehensive guide, it becomes clear that understanding the specific labeling needs of your product is crucial in choosing the appropriate labeling machine. The availability of such varied options ensures that for almost every labeling task, there is a machine perfectly suited to efficiently and effectively complete the job.