Have Any Questions?
Learn more about labeling machinery manufacturer. Below are general questions and answers about labeling machines from FAQ page. If you can’t find the information you need, please don’t hesitate to contact us directly.
General question
We’ve collected a list of questions that our users typically ask, and you can see for yourself if they answer your questions.
1. Are you machinery factory or trading company?
We are a manufacturing company specializing in labeling machinery since the 2000s. Our headquarters is based in Shanghai.
2. Where is your main market?
We export machinery to 110 countries. Our main markets are America, Russia, Europe, and the Middle East.
3. Which types of labeling machines do your factory have?
Our labeling machiney are divided into 3 categories: manual, semi-automatic, and fully automatic. And we have semi-automatic and automatic labeling machines, automatic machines include: cold glue labeling, hot glue labeling, self-adhesive labeling, and sleeve labeling machines.
4. How does a labeling machine work?
Labeling machines function by adhering labels onto products, employing various mechanisms depending on the type:
① Adhesive labeling machines
- The machine places the product on a conveyor belt, moving it to a specific position.
- When the product reaches the label peeling board, the detection sensor triggers a start signal, activating the main stepper motor.
- The motor pulls the label off the backing paper, and the gap between labels triggers the sensor to stop the motor, completing one labeling cycle.
② Sleeve labeling machines
- Products are placed on the machine, often via conveyor belts or positioning devices.
- Optical or inductive sensors detect the product size to ensure correct label placement.
- Labels are cut from a roll and prepared for application.
- The machine then slides the label over the product, secures it with brushes for stability, and ensures smooth application.
- After labeling, products move to the next station for further processing, like shrink wrapping.
5. Which types of industries can your labeling machines be used in?
In the food industry, our machines are suitable for labeling cans, boxes, bottles, and bags. In the beverage sector, they can apply labels to both bottles and cans.
For the cosmetic industry, our devices handle the labeling of products like lotion bottles and lipsticks. In the pharmaceutical field, they are perfect for labeling vials, syringes, and ampoules. In the packaging industry, our equipment is ideal for labeling both carton and bag packages.
Additionally, in the electronics industry, our machines can label the tops of electronic items as well as perform double-sided labeling of electronic components.
6. What types of surfaces can your labeling machines label?
Our machines can be applied to both smooth and solid surfaces.
7. Which shapes and product packaging are your labeling machines suitable for?
Our machines are versatile and can handle a variety of labeling needs. Below are some common applications for our labeling machines:
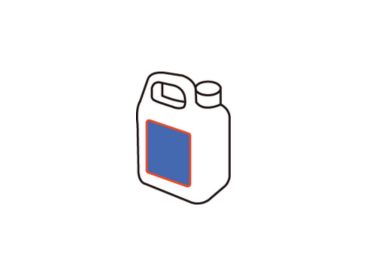
Sideways labeling on big containers
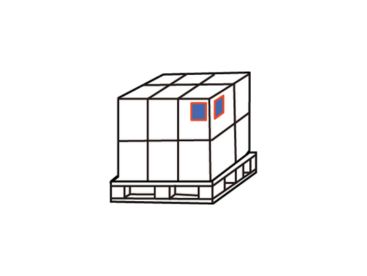
Labeling pallets – on one side, both sides
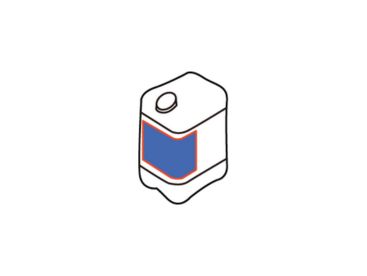
Labeling the corners of big containers
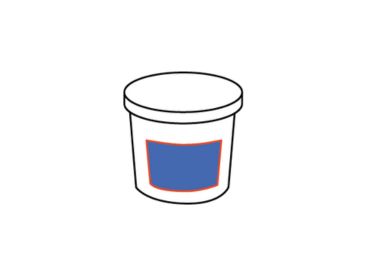
Labeling the sides of big, round products
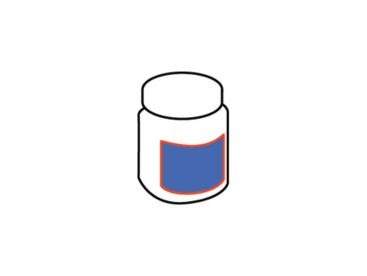
Labeling the sides of small, round products
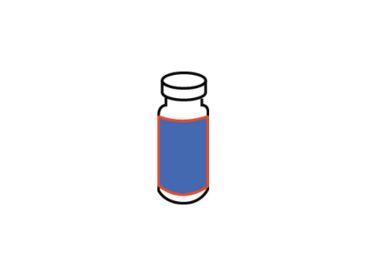
full wrap labeling of small, round products, as vial
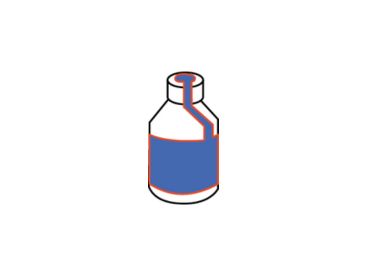
Secure labeling for products with round, cylindrical shapes.
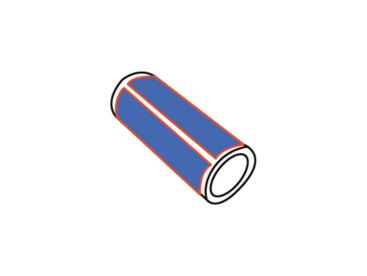
Complete wrap labeling of round, horizontal products
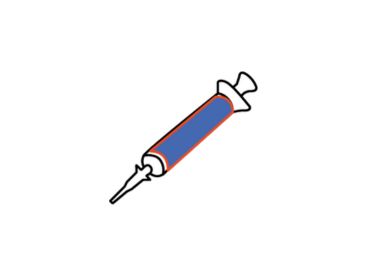
Comprehensive labeling of syringes.
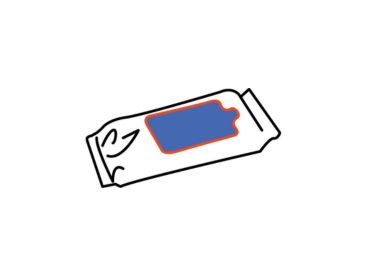
Labeling the top side of flat products
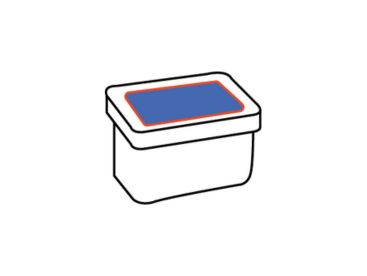
Labeling the top of tall products
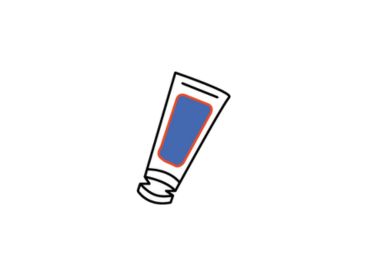
Labeling the top of tubes
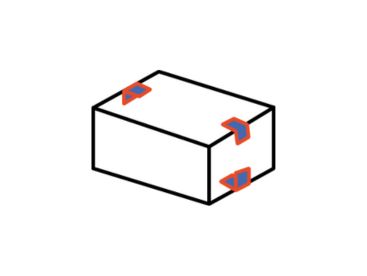
Tamper-proof labeling Seal labeling on rectangular products
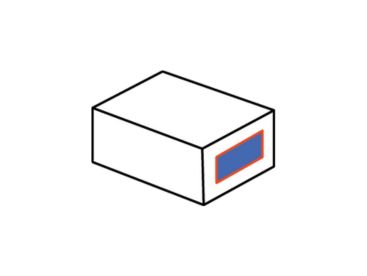
Side labeling of rectangular products
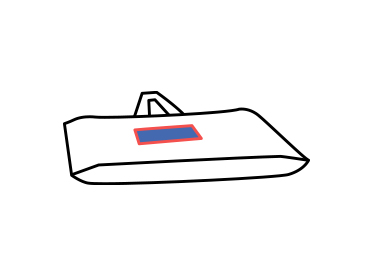
Labeling on the surface of plastic bags
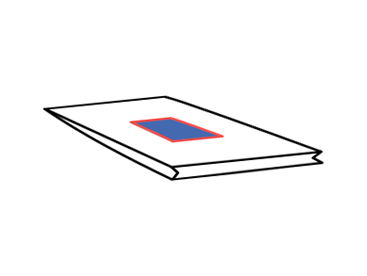
Labeling on the surface of paper bags
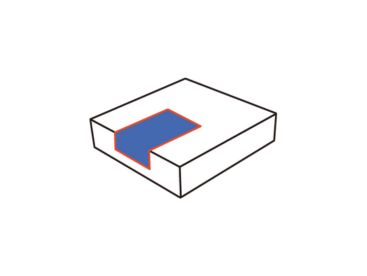
Double-sided labeling of flat objects
Whether you need a one-sided, two-sided, or wrap-around labeling machine, our labeling systems will meet your requirements. If you have specific needs, we also offer customized services to ensure your complete satisfaction.
Check these labeling machines below:
On the question of equipment failure
If you are experiencing problems with equipment failure, you can refer to the following:
1. Label break or label detection photoelectric abnormal!
Alarm reason: The object photoelectric gave the servo motor a start signal, but the label detection photoelectric did not timely give the servo motor a stop signal.
1) The label detection photoelectric signal is abnormal. Normally, the label should stop when the label detection photoelectric signal indicator light is on, and the label gap should stop when the label detection photoelectric signal indicator light is off. If the signal is abnormal, adjust the sensitivity.
2)Label detection was not performed. Redo the label detection and observe whether 2-4 labels appear during the detection process and whether the label length displayed on the operation screen is close to the actual value.
3)The label length setting is too long. If the label length value is set to the length of two or more labels. The label length should be reduced.
4)Label quality issues. Such as residual labels at the label gap or poorly connected label joints, etc.
5)The label output servo motor is damaged or the servo drive belt is broken. The motor action can be checked through system detection.
6)The label output clasp is not fastened properly. Fasten the label pulling clasp.
7)Label break. Connect the label and investigate the reason for the break.
2. Insufficient label stock!
1) Load a new label roll
2) Check the label stock photoelectricity for abnormalities.
3. Inverter alarm!
1) Determine the cause of the alarm by checking the alarm code on the inverter against the inverter manual. After troubleshooting, first press (OFF), then (OK), and finally (AUTO). Some alarms may require powering off the system before performing these steps to reset.
4. Servo motor error, Please power off!
1) Determine the cause of the error by checking the alarm code on the servo drive against the servo manual. The servo motor is locked and unable to turn when it is properly powered and stopped, with the servo drive displaying (run). Refer to the servo motor manual. After identifying the cause of the alarm and troubleshooting, cut off the main power supply and restart.
5. Label backing missing!
1) Adjust the position of the label detection photoelectric sensor.
2) Adjust the signal of the label detection photoelectric sensor. Refer to the sensitivity adjustment method of the label detection photoelectric sensor for how to adjust.
3) Label missing on the label strip. Use automatic or manual label advancement to move the labels until the label detection photoelectric sensor can detect them.
6. Label breakage
1) Check if the label-pressing sponge ring is too tight. Loosen it appropriately.
2) Check if the peeler plate edge is too sharp or has burrs. Sand the edge of the peeler plate with fine sandpaper.
3) The guide tape ring is too tight when limiting the label, damaging the label backing. Loosen the guide tape ring appropriately.
4) There may be an issue with the label. For instance, the label backing may have poor tensile strength or the die-cut is too deep.
7. Double labeling
1) Set the label dispensing length to the length of two labels.
2) The system was not checked after changing the labels.
3) There are residual labels at the label gaps.
8. Label wrinkling
1) The label is dispensed too early or too late; adjust the lateral position of the object’s photoelectric sensor.
2) The pressure exerted by the labeling mechanism on the product is not appropriate.
3) The carton is irregular.
4) The conveyor speed and the label dispensing speed do not match. Adjust the conveyor speed and label dispensing speed accordingly.
9. No label dispensing
1) The object’s photoelectric sensor has no signal. This can be determined by monitoring the input and output points through the I/O screen.
2) Servo motor fault.
About our services
If you have any questions about our services, you can refer to the following.
1. Is it feasible to receive a design that fits our facility’s unique layout?
Absolutely! Before finalizing your cost estimate, our engineering team is enthusiastic about crafting a design customized to the specifications of your facility, without any additional charge.
2. Can you provide references or case studies of previous clients who have used your labeling machines?
Certainly, we can provide references and case studies upon request. You can check these in our website.
3. What is the anticipated time frame for the delivery of our machine after an order is placed?
The arrival time of your machine can vary, depending on the specific model and our current production demands, but typically it takes about 6 to 8 weeks.
4. Can your labeling machine be integrated into our existing production line, and do you provide support for integration?
Our machines can design for integration into your existing production lines, and we provide full support during the integration process to minimize disruptions.
5. What payment methods do we accept?
We accommodate a range of payment methods to suit your preferences, including T/T, or L/C at sight.
6. What type of after-sales service do you offer?
Our commitment to your equipment extends over its entire life cycle. We provide consistent online support, ensure the availability of necessary parts, and perform regular maintenance to guarantee smooth operation.
7. Do you offer training for operating and maintaining the machine?
Indeed, we offer comprehensive online training sessions at no cost, designed to equip you with all the necessary skills and knowledge for the effective operation and upkeep of your machine.
8. What does the warranty for the machines cover?
Our machines are provided with a standard one-year warranty. You have the option to extend this warranty to enjoy longer coverage and added security.